Our Foundry
Our foundry is facilitated with different sections that are capable to handle a huge volume of material inflow without compromising on the quality aspect. Our foundry has mainly 5 different sections
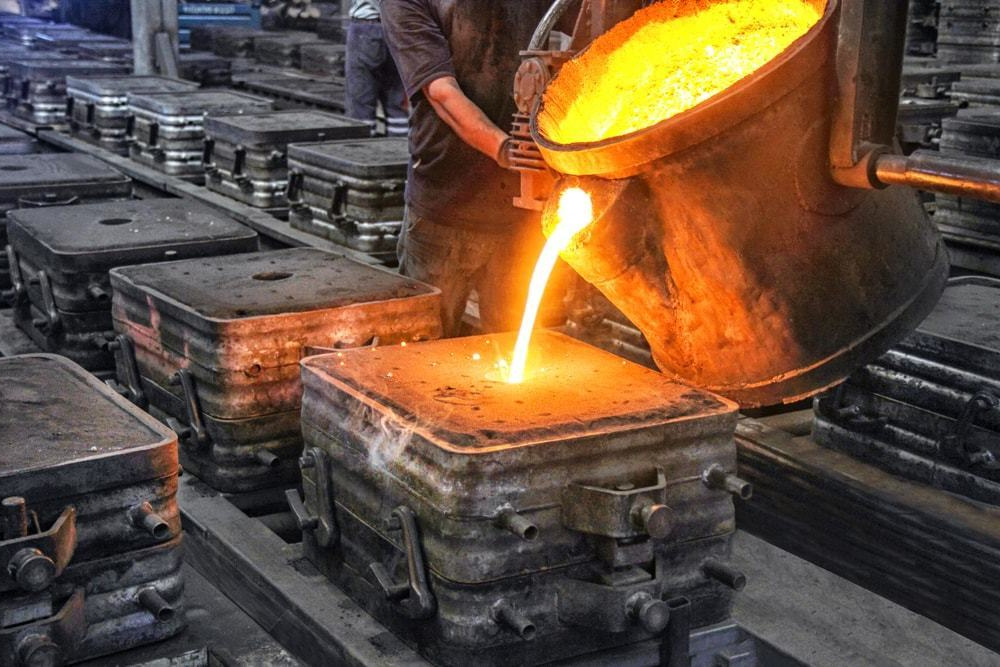
Moulding Section
As we all know the first step in creating the perfect product is by developing the mould. We are happy and proud to share that we are the first-ever foundry in India to develop the boxless No-Bake moulding method for wear resistance parts. This method is commonly known as shell core with air set moulding method.
Our workforce of highly skilled moulders can work from complex loose pattern equipment, particularly where low volumes are required, whilst our moulding line is suited for batch production.
Taking full advantage of the strength of the chemically bonded sand system, compact moulds provide a cost-effective method of manufacturing castings. Compact moulds are tailor-made to suit the component size ensuring that material used is kept to an absolute minimum. The no-bake method is recognised within the industry as offering the best surface finish and dimensional accuracy of any chemically bonded sand system currently available. Moulds are handled by skilled workers and flood coated to ensure that a superior surface finish and accuracy for which ADEPT METATECH Castings is renowned is maintained.
Small Boxless Moulding: – Casting weight range 4 – 20 kgs
Medium Boxless Moulding: – Casting weight range 25 – 40 kgs
When the component size is large for boxless moulding we have metal boxed sections that handle large components efficiently and safely. Where economically sized moulding boxes are used to result in reduced machining and finishing costs.
Medium Metal Box: – 50 – 250 kgs
Large Metal Box: – 250 – 400 kgs
Our advanced moulding section is equipped with a single-arm type continuous mixer for resin bonded sand with a capacity of 3 – 6 MT per hour. A close-loop moulding system is attached for the mixer with a range of 600 mm x 800 mm mould size on the compaction table.
Also, our moulding section houses an automated reclamation system with a capacity of 3 MT per hour. This system is a combination of three different operations that include knock out, sand cooler classifier and a pneumatic sand conveyor ( sand transporter ).
It is also home to 3 no’s of sand mix muller with an individual capacity of 500/750 kgs. Also, our core baking oven has a capacity of 1000 kgs.
Melting section
After the moulding section, the next process in the manufacturing of the product is the melting of the base raw materials. Our melting section consists of four medium frequency furnaces
- 250 KW 1000 HZ C/s IGBT base induction furnace with 500 Kg POT Capacity Box furnace crucible
- 150 KW 2000 HZ C/s IGBT base induction furnace with 200 Kg POT Capacity Box furnace crucible
- 100 KW 1500 HZ C/s IGBT base induction furnace with 100 Kg POT Capacity Box furnace crucible
- 100 KW 1500 HZ C/s IGBT base induction furnace with 100 Kg POT Capacity Box furnace crucible.
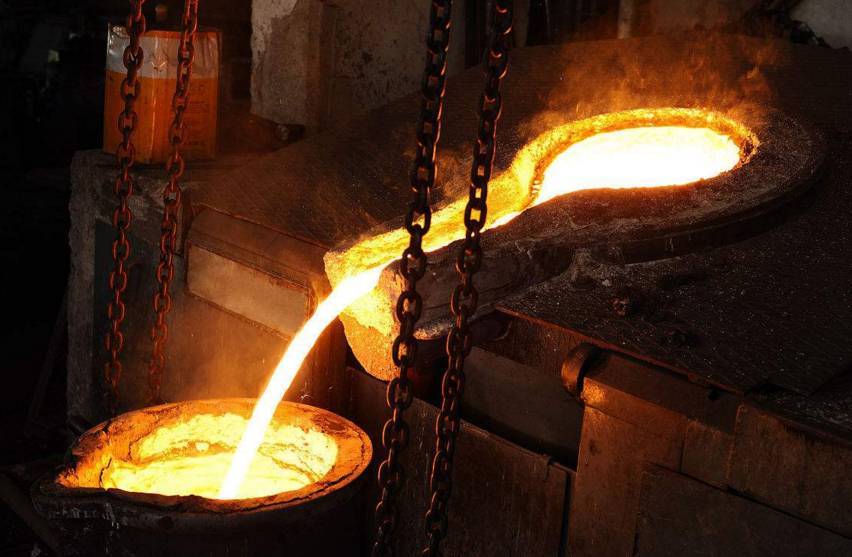
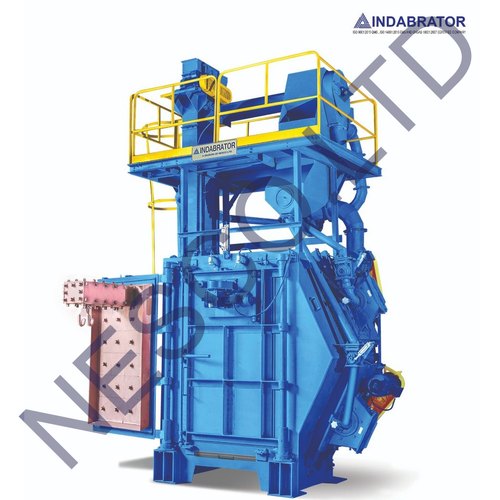
Shot Blasting
Shot blasting is the process by which unwanted sand particles are removed from the surface of the material by using abrasive shots. It has two-fold uses – it can be used for the surface finish as well as prior preparation of surfaces before further processing. Our plant has the Indabrator make 2 Wheel Spinner Hanger type Shot Blasting Machine.
Fettling
Fettling is the process that is used for removing the excess material from the parting line. Our foundry has a fettling section with specially skilled workers with the capability of 200 MT output per month, for that fettling section is equipped with swing grinders with 12” and 16” dia and flexible shaft grinders.
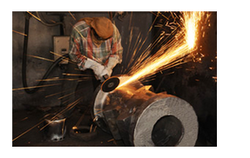

Heat Treatment
Heat treatment refers to the process where the metal is heated to modify the microstructure of the alloys. It is beneficial to increase the lifespan of the component. It can be used to increase the surface hardness, temperature resistance, ductility and strength. Our specialised heat treatment sections consist of 3 electric furnaces with a capacity of 1.5 MT, a PID controller with an auto programmer/ graph chart facility and a multi-point temperature recorder. It also has oil quenching and air quenching facilities with specially designed axial fans.